US Can Tap Into Rare Earth Production If China Halts Exports—But There’s a Caveat
Establishing a domestic supply chain to replace China’s dominance in processing rare earths could take as long as five years, a period crucial for producing essential components such as those found in iPhones and F-35 fighter jets.
While the United States possesses most of the 17 rare earth elements and 50 critical minerals underground, it lacks the industrial capacity to refine them into processed metals and magnets. This information comes from Melissa “Mel” Sanderson, a board member at American Rare Earths and co-chair of the Critical Minerals Institute.
“At present, there are no magnet manufacturers in the United States,” Sanderson informed The Epoch Times.
“I certainly hope that as the administration focuses on this vital sector—no pun intended—their awareness of this vulnerability gap, which spans four to five years for ramping up domestic production, will become apparent,” Sanderson stated.
Trump’s order from April 2 gives Commerce Secretary Howard Lutnick 180 days to recommend means for the federal government to bolster a “circular” domestic rare earth supply chain.
The president is also considering the possibility of an order that would allow for deep-sea mining and commercial stockpiling of resources.
According to economist Antonio Graceffo, industry will respond positively to policy changes involving permit reforms, deregulation, and public-private partnerships. He noted, “If China permanently bans the sale of rare earth minerals to the U.S., it could ultimately spur the U.S. to find alternative solutions.”
Graceffo, who analyzes U.S.-China trade relations for The Epoch Times, mentioned there are “numerous solutions” available for establishing a domestic rare earth supply chain, including ongoing negotiations with Ukraine.
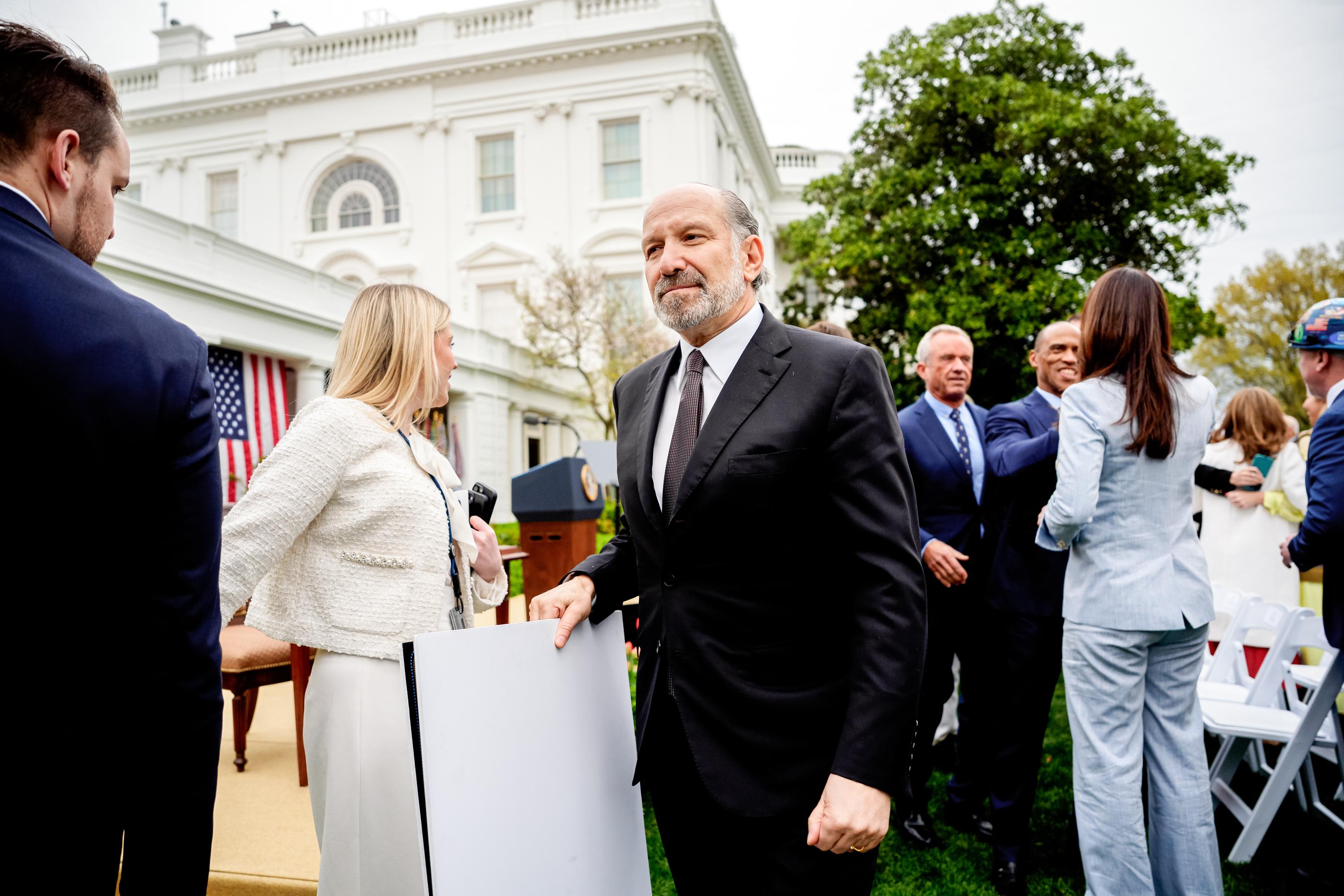
Commerce Secretary Howard Lutnick departs after President Donald Trump signs executive orders imposing tariffs on imported goods during an event in the Rose Garden at the White House on April 2, 2025. Trump announced sweeping new tariffs on imports from countries including China, Japan, and India. Andrew Harnik/Getty Images
“Absolutely, overcoming the challenges is possible,” he continued. “In the long term, if China cuts us off, it might force the U.S. to innovate.”
Colorado School of Mines economics professor Ian Lange shared a similar optimistic outlook. “Substitute materials exist for the seven restricted rare earths, and some manufacturers have indicated they can operate without them,” he noted.
He raised concerns about whether China can sustain its restrictions since American industries represent their largest market.
“We’ll have to determine if this is a real obstacle or just another hurdle we have to navigate,” Lange remarked to The Epoch Times. “There has been slow but steady progress in building up our supply chain over the last couple of years.
“We’re nearing the point of establishing something viable in the U.S.”
However, “close” is a relative term in the context of mining and refining, where proposed projects can often take anywhere from 10 to 20 years to gain approval.
‘Long Way Off’
American Rare Earths, an Australia-based company, is among a fleet of new ventures in the United States focused on rare earth and critical mineral mining.
The organization plans to refine dysprosium and terbium, two of the seven restricted “heavy” elements, by constructing a refinery adjacent to its Halleck Creek mine near Wheatland, Wyoming. Dysprosium is integral to magnets found in motors and generators for wind turbines, electric vehicles, and nuclear reactor control rods. Terbium compounds are widely applicable in electronics, semiconductors, and fluorescent lighting.
In Wyoming, Ramaco Resources is launching a pilot processing plant and developing an estimated 1.5 billion-ton rare earth deposit at their Brook Mine, while Rare Element Resources has initiated “proprietary processing and separation operations” at their Bear Lodge demonstration plant located in Upton.
USA Rare Earths, based in Oklahoma, is set to open a “neo-magnet” factory this year and has successfully produced its first dysprosium oxide sample from its Round Top mine in Texas, processing it at its research facility in Wheat Ridge, Colorado.
Ucore Rare Metals is also progressing with the development of the Louisiana Strategic Metals Complex in Alexandria, backed by $20 million in state incentives, while Energy Fuels, a uranium mining firm, is extracting rare earths from monazite sands at its White Mesa Mill in Utah. Both companies are Canadian-owned.
The leading players in the U.S. rare earth field are Australia’s Lynas Rare Earths, the largest developer outside China, and MP Materials Corp., based in Las Vegas.
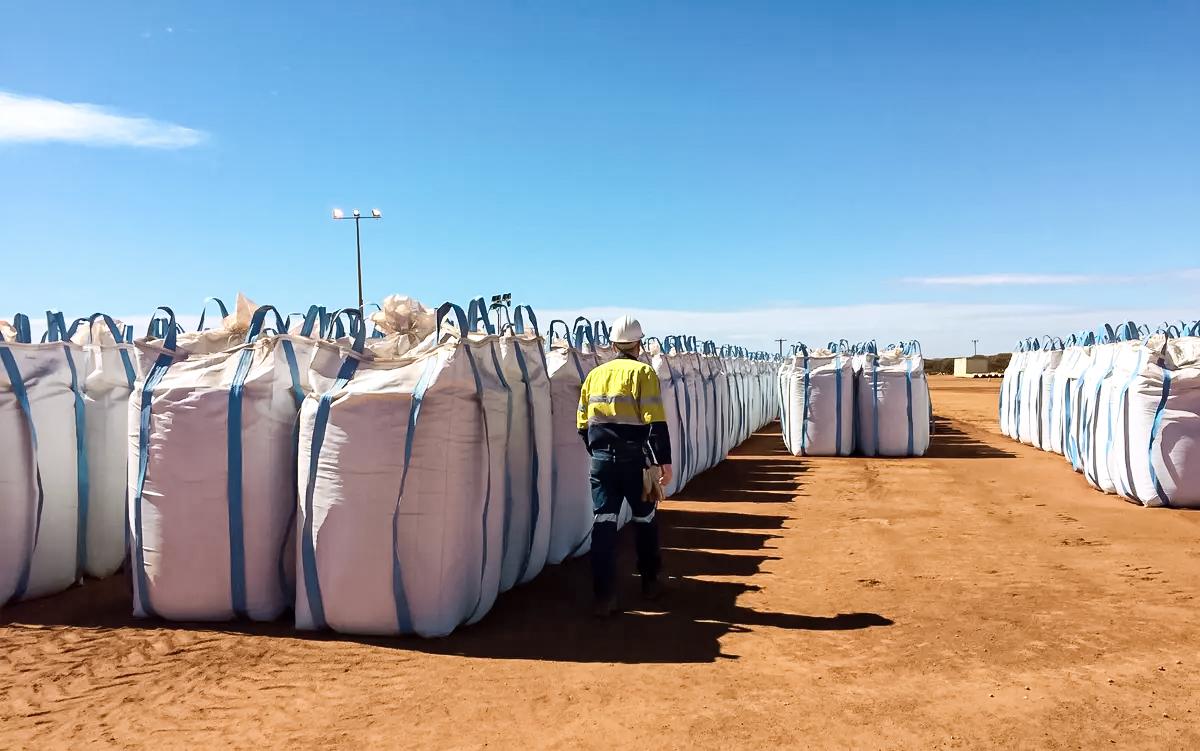
A Lynas Corp worker moves rare earth concentrate ready for dispatch to Malaysia at Mount Weld, northeast of Perth, Australia, on Aug. 23, 2019. Melanie Burton/Reuters
Both companies play critical roles in processing rare earths for the U.S. Department of Defense, which is currently developing a “sustainable mine-to-magnet supply chain” to fulfill its needs by 2027.
In January, the Pentagon stated it had expanded its initial project request beyond military requirements to bolster supply chain resilience, catering to both the emerging high-tech sector and national security needs.
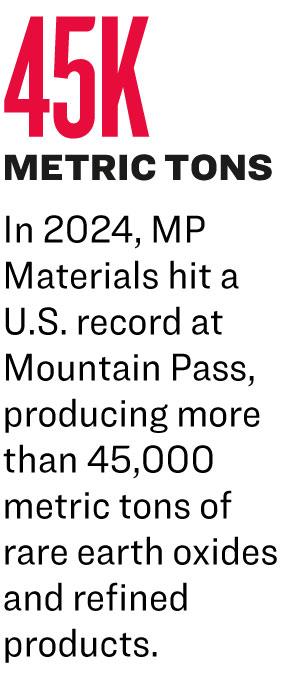
In 2024, with a record output at Mountain Pass, MP Materials delivered over 45,000 metric tons of rare earth oxides and refined products, including a historic 1,300 tons of neodymium-praseodymium oxide—essential components in “permanent magnets” recognized for their long-lasting magnetic properties.
“This milestone signifies a pivotal advancement in restoring a comprehensive rare earth magnet supply chain within the United States,” MP Materials CEO and founder James Litinsky remarked in January.
However, both Lynas Rare Earth and MP Materials extract considerably more rare earth ore than they can currently process. To maintain operations, they are required to export a significant portion of their excavated materials.
“Essentially, MP serves as China’s largest offshore supplier of rare earth ore,” stated Jack Lifton, Executive Chair of the Critical Minerals Institute, noting a purchase of 32,000 tons worth $350 million by China-based Shanghai Resources Industrial & Trading Co. from MP Materials in 2024.
MP Materials did not respond to inquiries for comment.
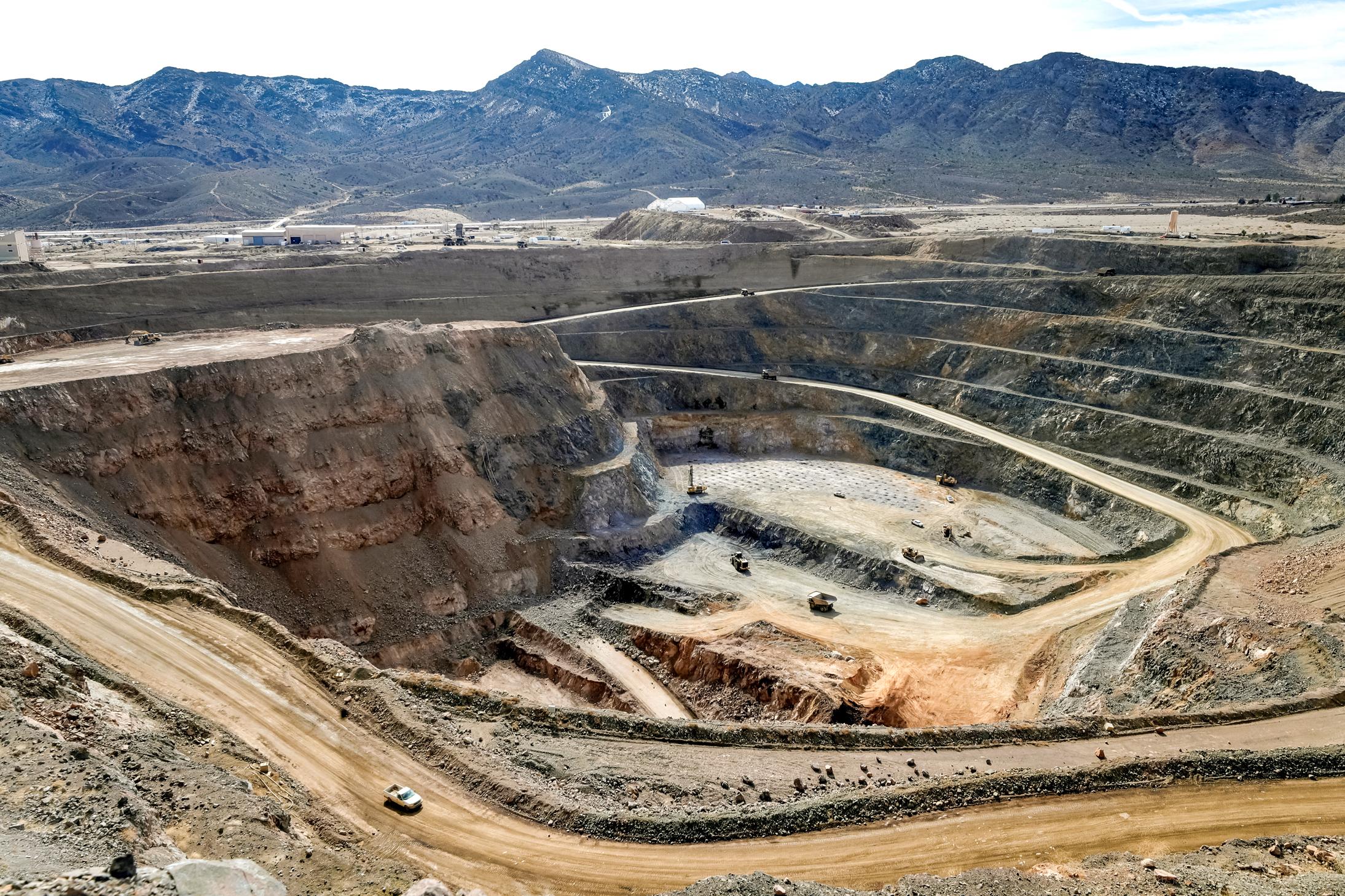
A view of the MP Materials rare earth open-pit mine in Mountain Pass, Calif., on Jan. 30, 2020. Steve Marcus/File Photo/Reuters
Imposing a 145 percent tariff on processed rare earth exports to the U.S. would be financially detrimental for China, according to Lifton. “It won’t be sustainable for them to maintain that pace, as it would cost them more than the value of the exports,” he indicated.
Meredith Schwartz, a research associate at the Center for Strategic & International Studies’s Project on Critical Minerals Security, pointed out that despite being the leading producer outside of China, Lynas still relies on China for refining due to its insufficient capacity.
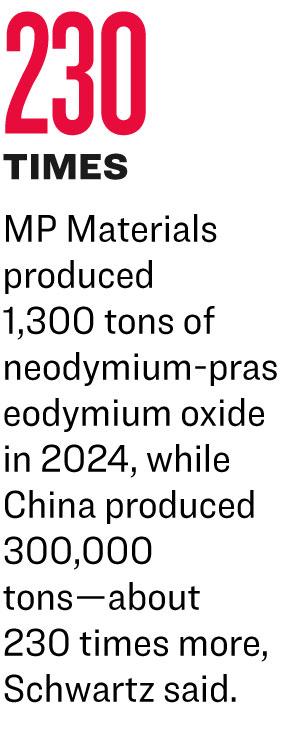
“Even with such facilities fully operational,” Schwartz explained, “they are not working near their commercial capacity and are dwarfed by China’s production volume.”
While MP Materials achieved an output of 1,300 tons of neodymium-praseodymium oxide in 2024, “China produced approximately 300,000 tons in the same year,” she added.
While progress is occurring, challenges remain. Schwartz highlighted that although USA Rare Earths hailed its first dysprosium oxide purification as a significant advancement for the domestic rare earth sector, transitioning sample production from the lab to full-scale commercial output still demands considerable effort.
“Despite the recent investments, the United States is still a long way from achieving the [Department of Defense’s] objective of a mine-to-magnet supply chain that’s independent of China, let alone rivaling foreign adversaries in this strategically critical industry,” she asserted.
“The development of mining and processing capabilities will require a long-term commitment, ensuring that the U.S. remains at a disadvantage for the foreseeable future.”
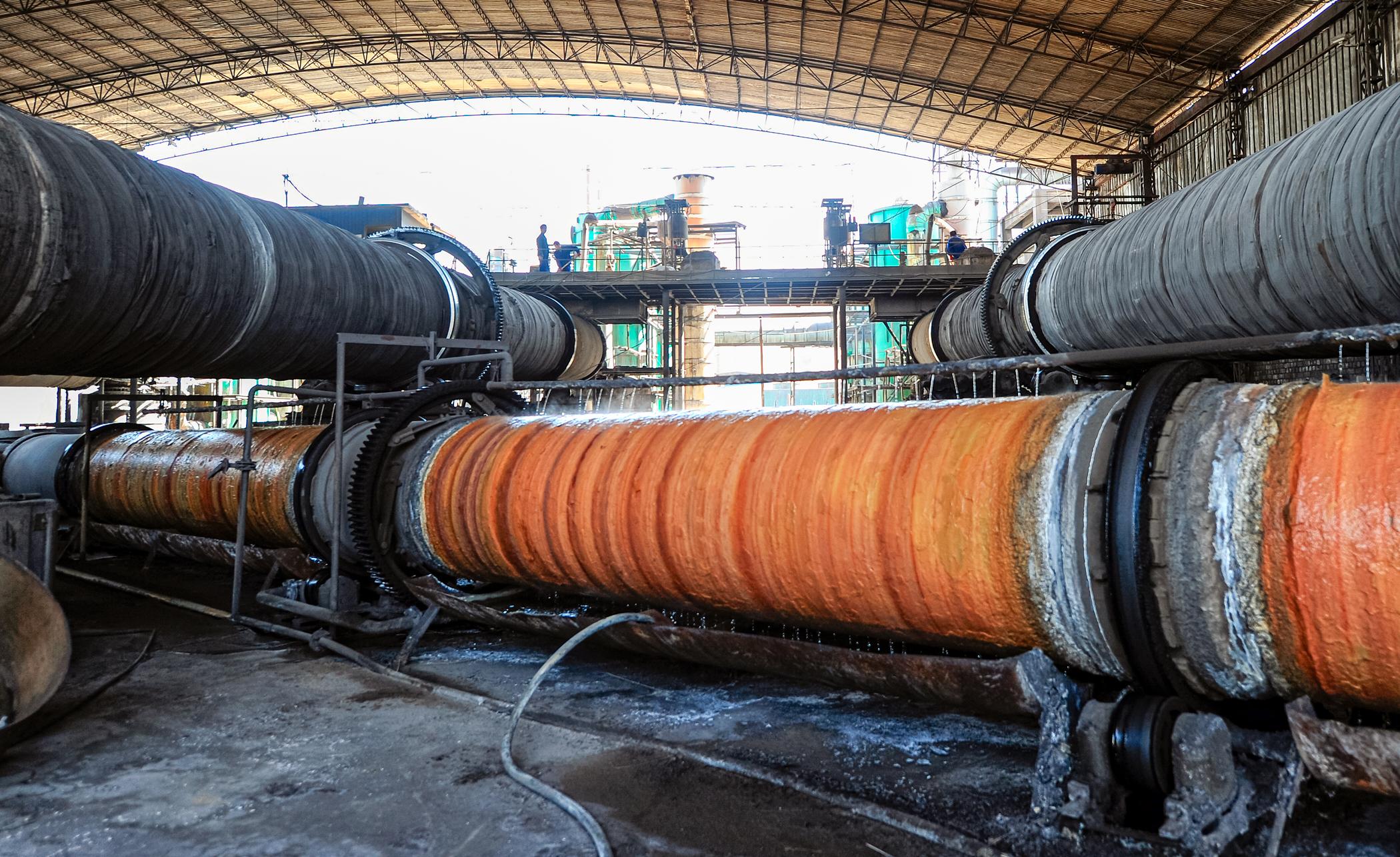
Rare earths cooling in dripping water within steel pipes at a processing facility in Baotou, Inner Mongolia, on April 21, 2011. The area houses numerous processing plants, where local farmers have reported destruction of their livelihoods due to toxic waste resulting from rare earth and coal production. Residents near the tailings dam—a six-square-mile toxic waste expanse—also report severe health issues, with tests revealing elevated levels of radioactive contaminants in nearby soil and water. Frederic J. Brown/AFP via Getty Images
Estimating timelines in rare earth development is also complex due to many variables. “Any timeline a company provides—regardless of the industry—is typically just a best-guess estimate based on optimistic conditions: stable supply chains, manageable costs, favorable weather, and so on,” she explained.
Nevertheless, Lifton expressed optimism regarding the potential for funding, given the more than $400 billion in tax credits and incentives associated with the 2022 Inflation Reduction Act—at least for the time being.
Leseur emphasized that establishing a domestic rare earth supply chain will require time, underscoring the importance of proceeding correctly.
“Can it be completed quickly? No,” he affirmed. “Can it be done sustainably? Yes. It necessitates time as many of these initiatives—like American Rare Earth’s Halleck Creek mine—are greenfield developments, starting from the ground up.”
Currently, the nation’s rare earth industry is “merely small-scale operations in a vast landscape,” Sanderson remarked. “Yet, one must start small to achieve growth, correct?”